The Scientific Research Behind Porosity: A Comprehensive Overview for Welders and Fabricators
Comprehending the complex devices behind porosity in welding is critical for welders and producers aiming for remarkable workmanship. From the composition of the base products to the intricacies of the welding process itself, a plethora of variables conspire to either aggravate or minimize the existence of porosity.
Comprehending Porosity in Welding
FIRST SENTENCE:
Examination of porosity in welding discloses vital understandings right into the stability and top quality of the weld joint. Porosity, defined by the existence of dental caries or gaps within the weld steel, is a typical worry in welding procedures. These gaps, otherwise effectively addressed, can jeopardize the architectural integrity and mechanical buildings of the weld, causing potential failings in the completed product.
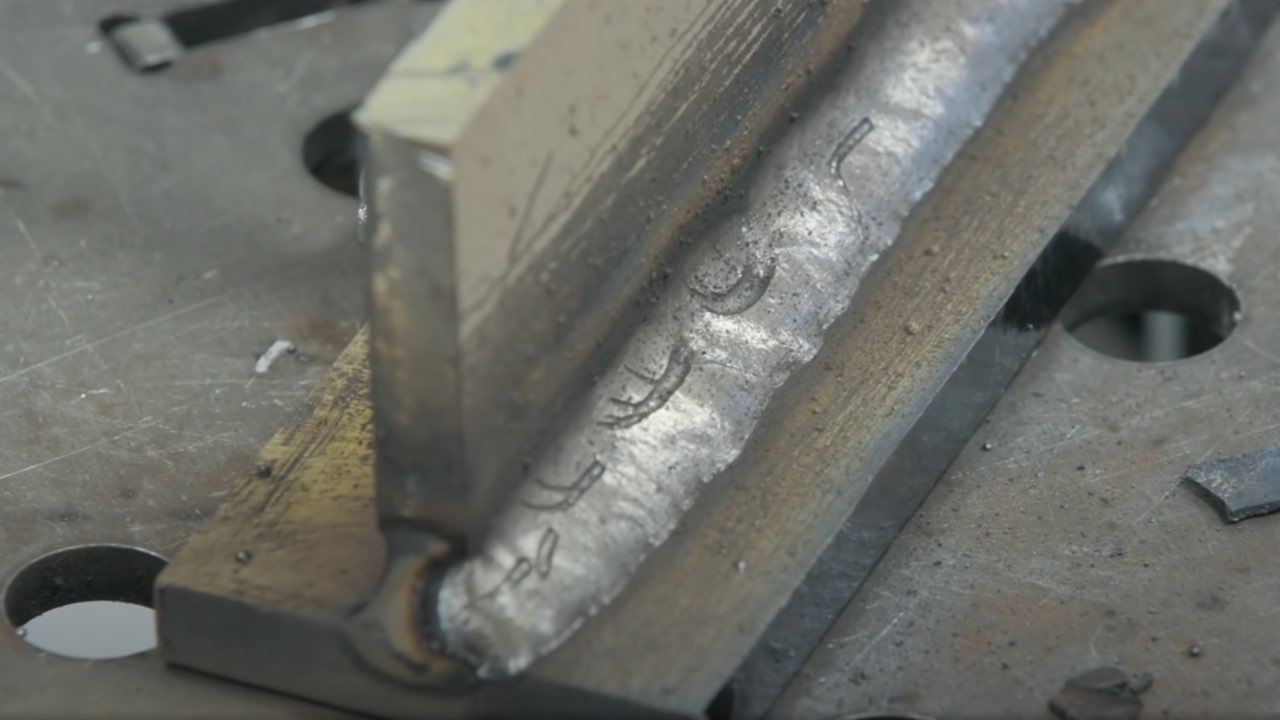
To find and measure porosity, non-destructive testing methods such as ultrasonic testing or X-ray evaluation are often utilized. These methods permit for the identification of inner issues without compromising the stability of the weld. By analyzing the dimension, shape, and distribution of porosity within a weld, welders can make enlightened decisions to boost their welding procedures and attain sounder weld joints.
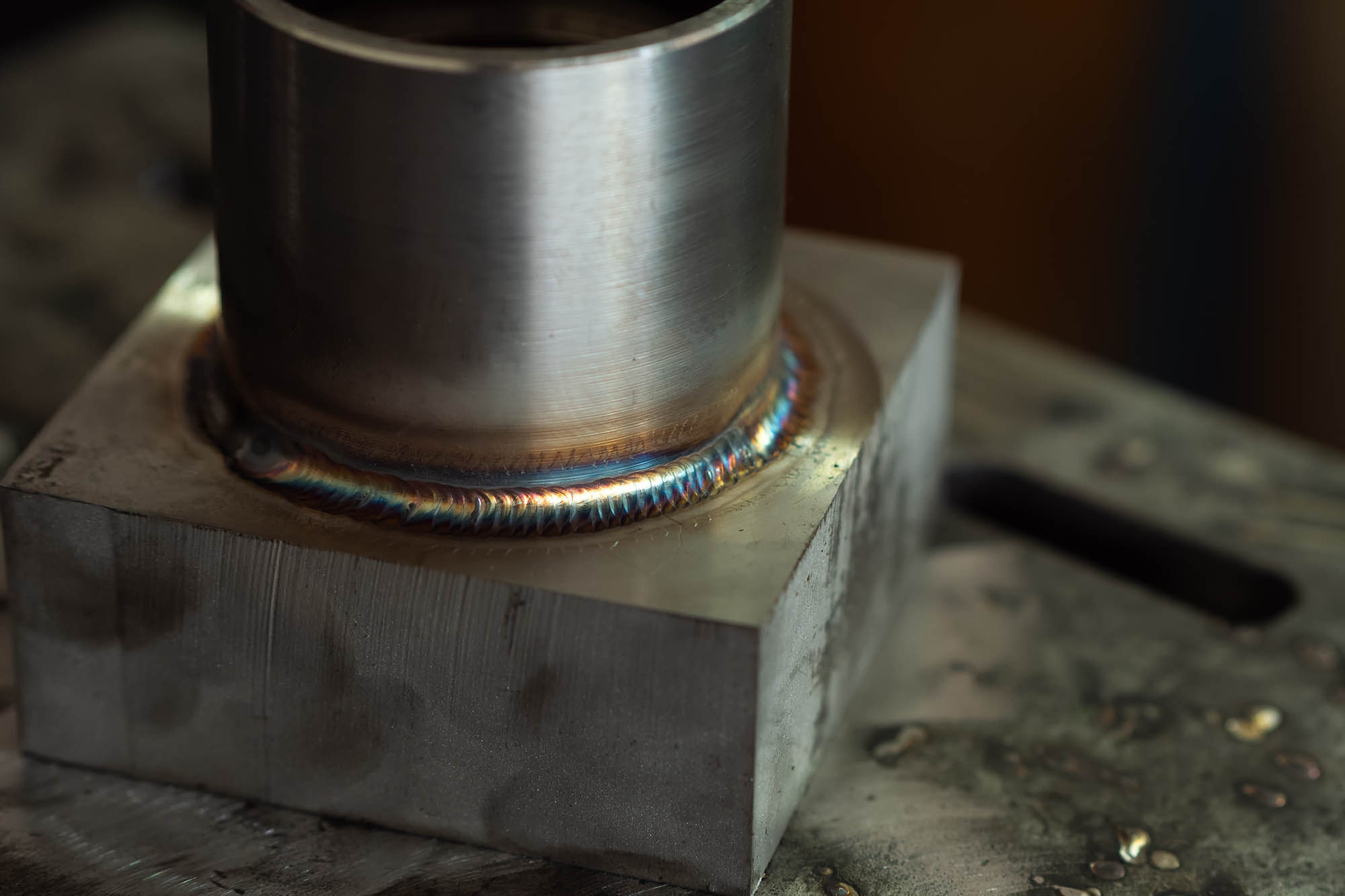
Elements Influencing Porosity Development
The occurrence of porosity in welding is influenced by a myriad of variables, varying from gas shielding effectiveness to the intricacies of welding specification setups. One important factor contributing to porosity formation is insufficient gas securing. When the shielding gas, normally argon or carbon dioxide, is not efficiently covering the weld pool, atmospheric gases like oxygen and nitrogen can infect the molten metal, causing porosity. Furthermore, the tidiness of the base materials plays a significant function. Pollutants such as corrosion, oil, or dampness can vaporize during welding, creating gas pockets within the weld. Welding specifications, including voltage, present, take a trip speed, and electrode type, also influence porosity development. Using incorrect settings can produce excessive spatter or warmth input, which consequently can lead to porosity. The welding strategy utilized, such as gas metal arc welding (GMAW) or secured metal arc welding (SMAW), can influence porosity formation due to variants in a knockout post warmth circulation and gas coverage. Recognizing and managing these elements are important for reducing porosity in welding procedures.
Effects of Porosity on Weld Top Quality
Porosity development dramatically jeopardizes the architectural stability and mechanical buildings of bonded joints. When porosity is existing in a weld, it develops gaps or dental caries within the material, reducing the overall stamina of the joint. These voids serve as tension concentration points, making the weld more prone to splitting and failing under lots. The presence of porosity additionally compromises the weld's resistance to rust, as the caught air or gases within the voids can respond with the surrounding environment, resulting in destruction over time. Additionally, porosity can impede the weld's capability to hold up against pressure or impact, more threatening the total quality and integrity of the welded structure. In essential applications such as aerospace, auto, or architectural constructions, where security and toughness are critical, the destructive results of porosity on find out here now weld quality can have extreme effects, emphasizing the importance of decreasing porosity via appropriate welding techniques and procedures.
Methods to Minimize Porosity
In addition, using the suitable welding specifications, such as the proper voltage, present, and take a trip speed, is critical in avoiding porosity. Preserving a consistent arc length and angle throughout welding likewise assists minimize the possibility of porosity.

Furthermore, choosing the best securing gas and preserving correct gas circulation prices are crucial in minimizing porosity. Making use of the appropriate welding technique, such as back-stepping or employing a weaving activity, can also help disperse warm equally and decrease the chances of porosity development. Finally, making certain appropriate ventilation in the welding environment to get rid of any kind of possible sources of contamination is crucial for attaining porosity-free welds. By implementing these techniques, welders can properly decrease porosity and create top notch bonded joints.
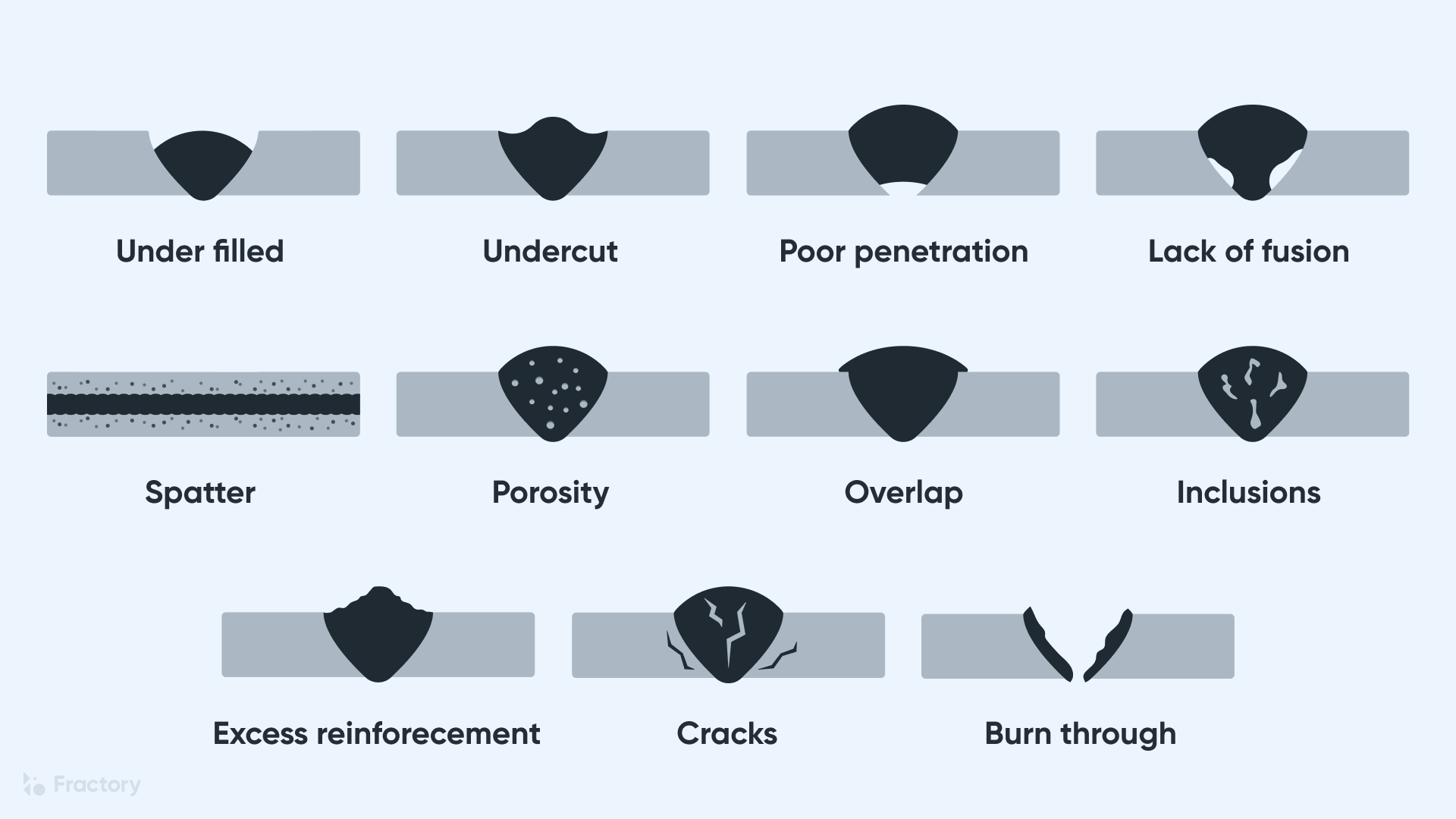
Advanced Solutions for Porosity Control
Carrying out innovative technologies and cutting-edge techniques plays an essential duty in achieving remarkable control over porosity in welding processes. Furthermore, employing sophisticated welding strategies such as pulsed MIG welding or customized atmosphere welding can also assist mitigate porosity concerns.
An additional innovative service entails the use of innovative welding tools. Using equipment with built-in functions like waveform control and sophisticated power sources can improve weld top quality and minimize porosity risks. The application of useful source automated welding systems with exact control over parameters can significantly minimize porosity defects.
Moreover, integrating innovative tracking and inspection technologies such as real-time X-ray imaging or automated ultrasonic testing can aid in discovering porosity early in the welding procedure, enabling for immediate corrective activities. Overall, incorporating these innovative options can significantly improve porosity control and enhance the total high quality of welded components.
Conclusion
To conclude, recognizing the science behind porosity in welding is vital for welders and makers to create high-grade welds. By recognizing the aspects affecting porosity development and carrying out techniques to minimize it, welders can improve the general weld quality. Advanced options for porosity control can further boost the welding process and make certain a solid and trusted weld. It is very important for welders to continuously inform themselves on porosity and apply ideal techniques to attain optimum outcomes.